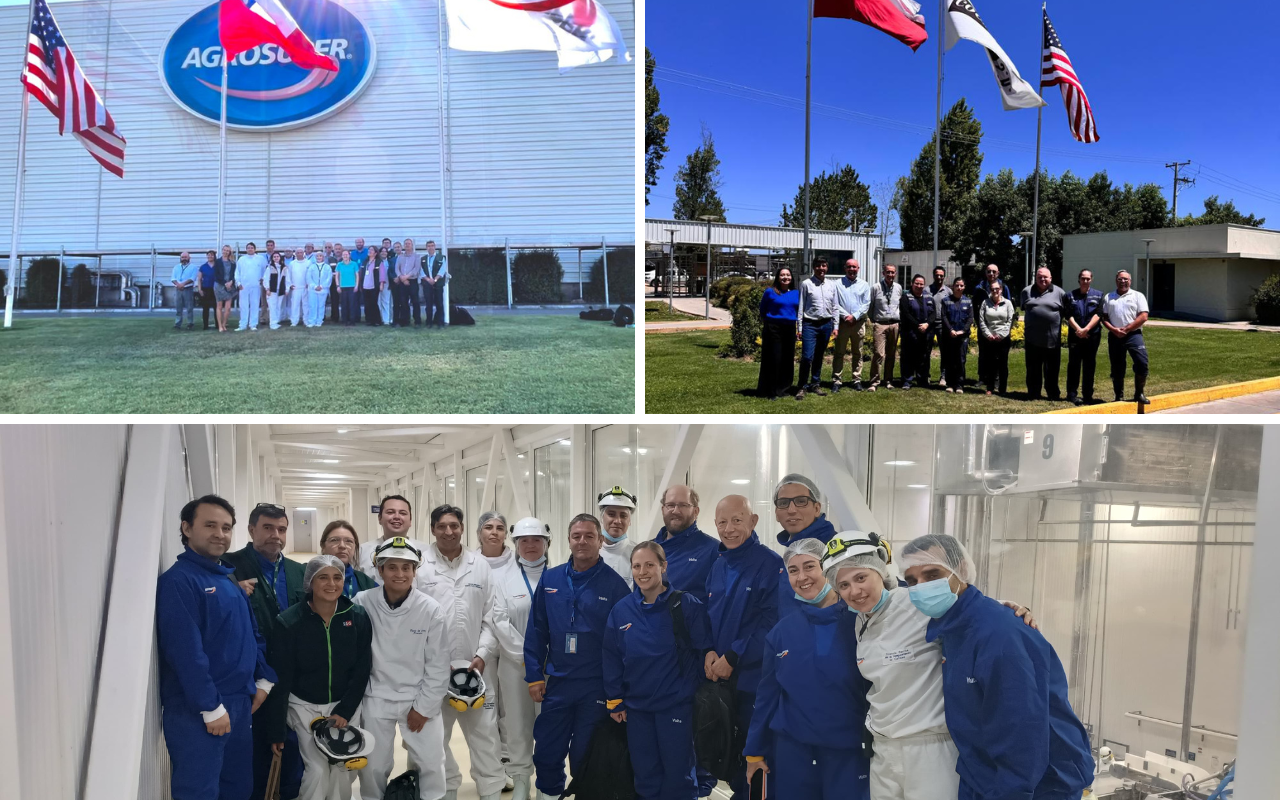
FSIS audit positively assesses Chilean plants
Last January, an audit by the United States Department of Agriculture (USDA) Food Safety and Inspection Service (FSIS) assessed the Agricultural and Livestock Service (SAG) meat inspection and certification system -supported by the meat export sector to verify compliance with U.S. regulations. Chile, Canada, Mexico, and Poland are the only four countries cleared to export […]
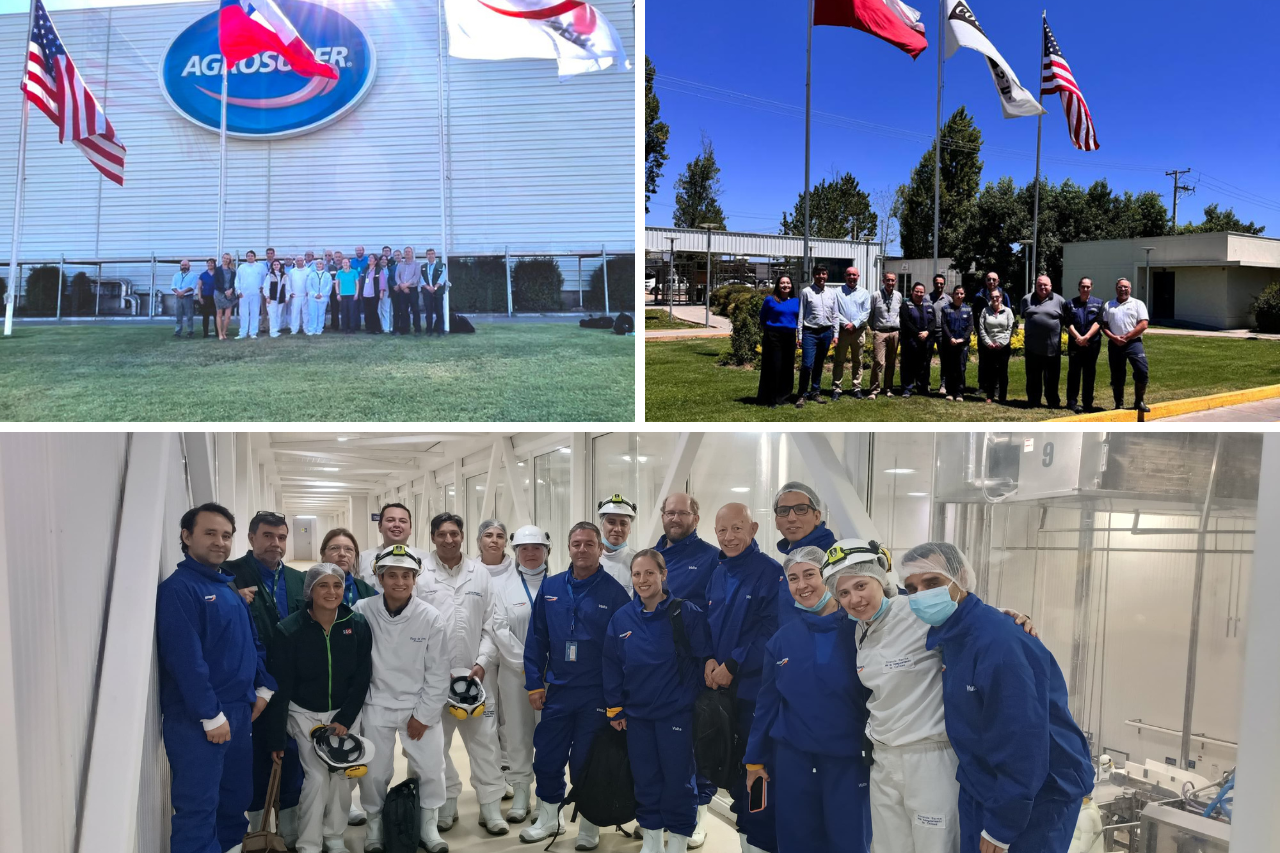
Last January, an audit by the United States Department of Agriculture (USDA) Food Safety and Inspection Service (FSIS) assessed the Agricultural and Livestock Service (SAG) meat inspection and certification system -supported by the meat export sector to verify compliance with U.S. regulations.
Chile, Canada, Mexico, and Poland are the only four countries cleared to export raw chicken to the United States. This is not a random decision, but the fruit of strict compliance with the world’s highest standards.
Chile maintains access to the U.S. market thanks to a regular international auditing process that validates the country’s food safety system, assuring the quality of its chicken and pork exports. The final results of the latest audit conducted by FSIS from January 27 to February 7 will be reported in the coming months. The goal of the audit is to ensure that Chilean meat production complies with U.S. regulations to maintain the authorization to export to this demanding market.
How does the U.S. authorization system work?
Each international inspection not only guarantees access to highly demanding markets but also reinforces Chile’s reputation as a reliable global supplier. The FSIS audit assesses Chile’s performance in multiple areas, including poultry, pork, cattle, and lamb slaughterhouses, packing plants, official and private laboratories, and SAG’s headquarters and regional offices.
The visit covered Sopraval, Las Pataguas, Procesadora de Alimentos del Sur, San Vicente, Lo Miranda (chicken), and Coexca slaughterhouses, plus Preciza Frozen’s packing plant, and the Merieux Nutrisciences (microbiological analysis) and Eurofins (drug residues and contaminants) laboratories.
The structure of the U.S. audit is key to understanding how Chilean meat production is inspected. There are two types of certifications: Delegated and direct. Chile has a delegated system, meaning that FSIS audits SAG to verify that it is fulfilling its oversight role over the industry. In contrast, Mexico uses a direct certification system, meaning that foreign inspectors must travel to Chile to audit and approve each individual plant.
The U.S. model allows SAG to be directly responsible for local inspections under U.S. standards, allowing Chile to autonomously manage its exports.
Technical preparation
The success of these audits depends on the coordinated work between the public and private sectors. ChileCarne plays a critical role as a facilitator, ensuring that the slaughterhouses are well prepared for the evaluation process. This translates into support for the company and active participation in workshops, seminars, and international conferences, all to anticipate any regulatory changes and stay up to date with global health requirements, among other things.
Before each international audit, companies are provided with the latest regulations and checklists, undergo internal audits, and train their quality assurance teams. A critical aspect during this phase is analyzing previous audit reports to identify opportunities for improvement and ensure that previous issues have been corrected.
On site, ChileCarne joins the inspector to gather first-hand information of their assessments.
This proactive approach has strengthened the capacity of Chile’s health and food safety system to successfully undergo international inspections and maintain access to strategic markets. On average, the chicken and pork export sector undergoes three or four market audits per year; the key lies in preparation and ongoing learning.
Beyond compliance: impact on international trade
Since the inspections went smoothly, no critical findings were reported following the exit meeting. This reinforces the robustness of Chile’s inspection and certification system, and SAG’s excellent work in verifying compliance with U.S. regulations, which is critical to preserve the trust of such strategic markets.
For example, in 2024 Chile exported 46,000 tons of chicken and 3,000 tons of pork, representing $145 million USD and $11 million USD, respectively. This makes the country the second-largest chicken exporter to the United States, after Canada, and the twelfth largest pork exporter.
In times where food safety is a critical factor in international trade, Chile continues to cement its leadership by meeting the highest standards that guarantee quality, safety, and reliability in every shipment.